STONE 40A-L V2.0
- Industrial-grade professional procedures, safe and reliable
- Highly reliable start algorithm, no fear of headwind starting
- The throttle is anti-phase loss and fast throttle response to reduce the risk of crashes
- Highly intelligent, adaptive working parameters
- Secure matching
- Specification: 40A 4~6S
- Retail Price: ¥229
Features
- Multiple protection safety: low voltage protection, high voltage protection, start protection, locked-rotor protection, over-temperature protection, over-current protection, overload protection, runaway protection
- The direction of rotation can be set by software
- High-quality components, reliable performance, low internal resistance, MOS, instantaneous current resistance
- The serial port outputs real-time data such as power supply voltage, motor speed, current, ESC temperature and debugging data.
- Shielding signal lines reduces interference
- Optoelectronic isolation signal input and output interfaces isolate interference
- Waterproof Rating: IP55 / Customizable IP68
- Lightweight design, simple and easy to use, stable and reliable, strong anti-interference ability, good speed regulation performance
Multiple security features
Low voltage protection: off by default (can be customized on).
High voltage protection: prohibit the motor from starting when the power supply voltage exceeds the allowable value.
Startup protection: If the startup is unsuccessful, the startup current will be limited, and the startup will be restarted automatically.
Stall protection: If a stall occurs during normal operation (usually caused by external force), try to restart (note that the stall may damage the ESC when the throtor is high).
Over-temperature protection: When the temperature exceeds 125°C, the maximum output power is slowly reduced, up to 40% of the full throttle power, and the original power is restored after the temperature is reduced.
Over-current protection: limit the peak current and do not exceed the limit value.
Overload Protection: When an overload is identified on the motor, the maximum throttle is limited to protect the powertrain.
Loss of control protection: 200ms after the loss of signal gradually reduce the output power, in 1~2 seconds for rapid throttle reduction to less than 50%, and then slowly reduce the throttle to stop.
Basic parameter
Model:STONE 40A-L V2.0
Lithium support:4~6S (higher than 30V prohibits startup)
Continuous operating current: 40A (specific heat dissipation conditions)
Instantaneous operating current (less than 3 seconds):60A
Product Dimensions:51*47.5mm
ESC Weight:32.2g
Waterproof rating:IP55
Throttle travel range:1000~2000us(Default)
BEC Output:not
Input signal level:3.3~5V
Temperature protection points:125℃
Operating ambient temperature:-20~+65℃
Communication methods:PWM
Preservation Temperature:-10~+40℃
Throttle response time:200ms (default, customizable)
Throttle Refresh Rate:50~500Hz (100~400Hz recommended)
- Throttle Response Time: When the ESC receives 10%~100% step throttle, the throttle reaches the maximum value within the specified time, but usually the motor speed lags the throttle by 100~150ms.
- Performance parameters can be customized according to customer needs, including but not limited to protection temperature, response time, etc.
Instructions for use of the STONE series
Disclaimer:
Thank you for using this product! The brushless power system is powerful, and incorrect use can cause personal injury and equipment damage. For this reason, we strongly recommend that you read this manual carefully before using the device, and we do not assume any liability arising from the use of this product, including but not limited to compensation for incidental or indirect losses; At the same time, we do not assume any responsibility arising from unauthorized modification and incorrect use of the product. We reserve the right to change the design, appearance, performance and use requirements of our products without notice.
Interface definition

Wiring
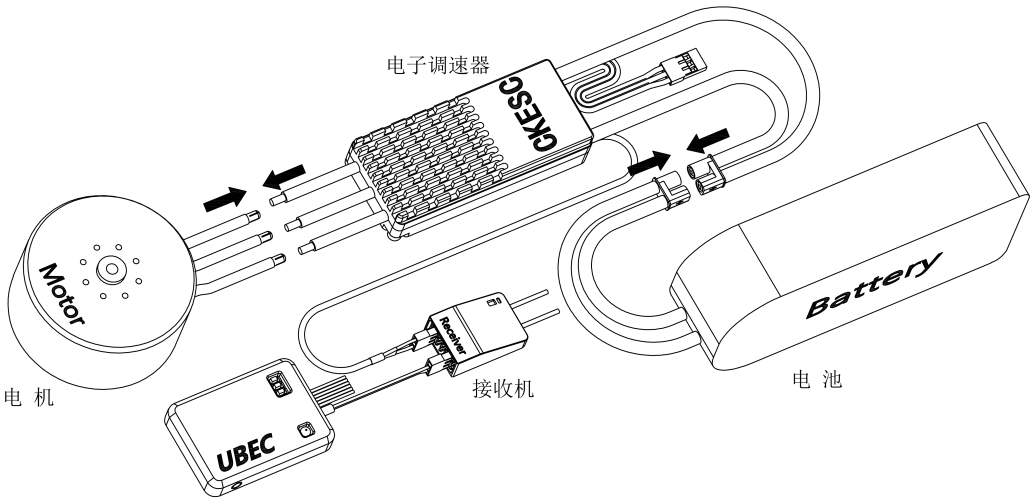
Throttle correction
- Adjust the throttle signal to the maximum value, turn on the power to start the throttle calibration, the motor will emit “♪123-3-3-3″, and immediately after that, adjust the throttle signal to the minimum value, the motor will emit the music ”♪3-3-5-4″, after the music is finished, the throttle stroke calibration is completed.
- Throttle travel must be calibrated for accurate control before using or replacing the remote control (throttle signaling device) for the first time.
Data output
Data output adopts 3-wire UART-TTL, baud rate 38400bps, character mode.
Packet format:SPD:XXXX TMOS:XXXX TMOT:XXXXTMCX:XXXXXXXXXXXXXXXXXX CURI:XXXX VOLT: XXXX PWAC:XXXXX SYS:XXXXXXXXXXXX DBG:XXXXXXXXXXXX
Of which.
SPD:XXXX Motor speed (RPM, error ±12RPM, converted according to the number of motor poles 42P)
TMOS:XXXX ESC temperature (°C, error ±1°C)
TMOT:XXXX Motor temperature (°C, error ±1°C, data retained)
TMCX: XXXXXXXXXXXX (debugging data)
CURI:XXXX Motor current (X0.01A, error ±10%, mainly used for ESC overcurrent protection)
VOLT:XXXX Power supply voltage (X0.01V, error ±0.5V)
PWAC: XXXX (debugging data)
SYS:XXXXXXXXXXXX (debugging data)
DBG:XXXXXXXXXXXXX : (debugging data)
Fault phenomenon
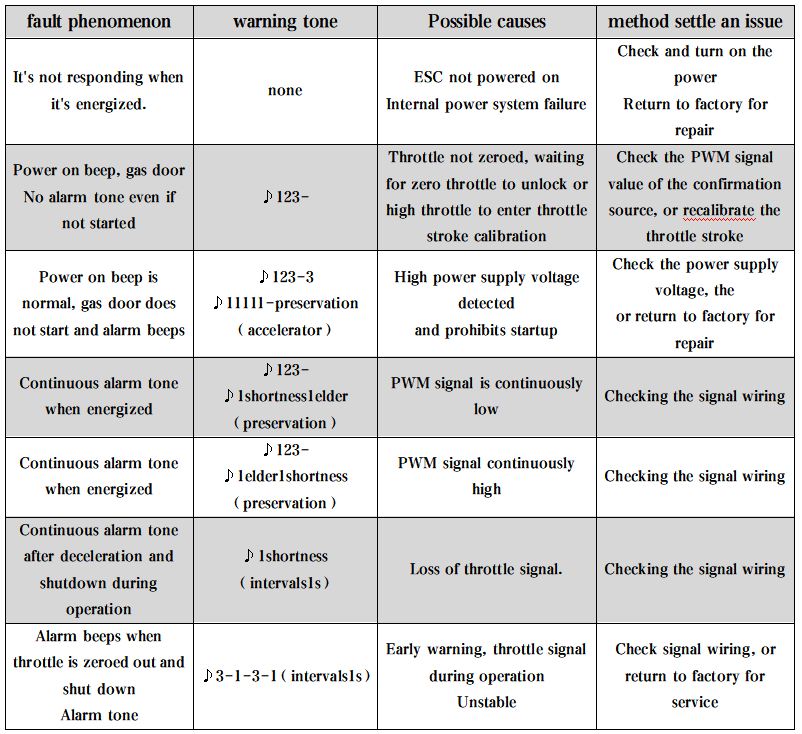
Safety Notice
The signal pulse width and frequency must meet the requirements. Do not pull and plug the control signal cable with electricity, and ensure that the ESC signal cable is connected reliably and not loose, so as to prevent the production of interference signals and cause abnormal control.
You can use an anti-ignition plug for the power connection, but make sure that the connection is reliable (a poor connection can lead to plug ablation and even power failure); Do not use an anti-ignition plug for the output phase cable, and do not plug and unplug it with electricity. Make sure that the power supply voltage is stable (if it is battery powered, pay attention to the high discharge rate of the battery and good low-temperature discharge performance), otherwise it may cause damage to the ESC.
Ensure that the ESC has good heat dissipation, and long-term operation of the ESC at high temperature will accelerate the aging of components and greatly reduce the service life of the ESC. It is recommended to monitor the working temperature in real time, and judge whether the current working conditions are safe according to the real-time output temperature data (the temperature is safer than 100°C, higher than 100°C is poor heat dissipation or excessive load, and more than 115°C is not safe).
Do not short-circuit the output phase line before the residual power of the ESC is exhausted, which may cause damage to the ESC.
When this product is applied to aircraft, the following matters should be noted:
(1) Please use a reasonable configuration with an ESC to get the best performance (power efficiency, power, safety). Using mismatched motors, propellers (not even propeller loads or variable loads), or incorrect voltages can result in suboptimal performance or even damage to the ESC.
(2) Before each flight, it is recommended to check whether the structure of each part of the aircraft is loose, aged or damaged, and the arm and propeller fixing screws must be locked firmly.
③ Be sure to use a stable load, the propeller should be blocked by the external throttle should be closed as soon as possible or disconnected to prevent blocking the current is too large and damage to the ESC is strictly prohibited overloading, otherwise the product performance and safety will not be guaranteed.
Please do not disassemble and modify the product without authorization, otherwise the performance and safety of use and warranty service cannot be guaranteed.